
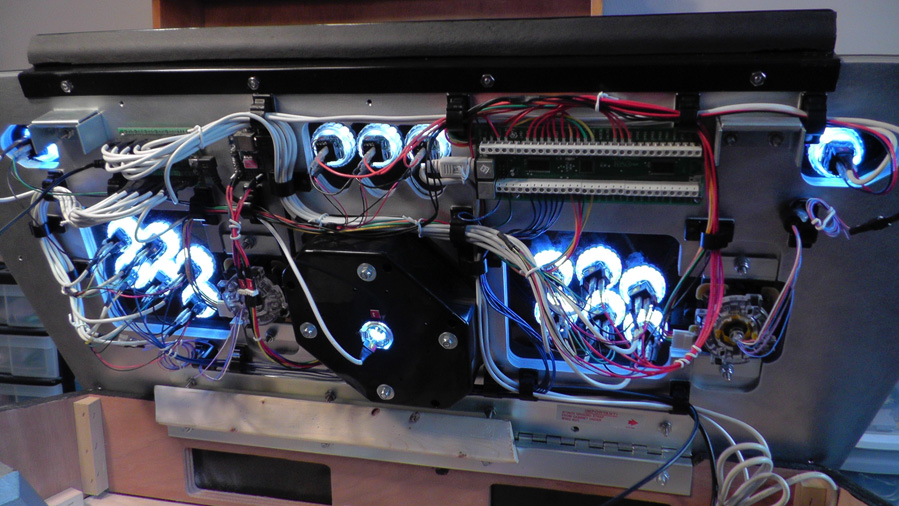
To be honest I’m not sure how people normally mount these joysticks but this method worked for me. You can see what I mean by the pictures below. It worked pretty well as it was a slightly spongy material in the end and cushioned the joystick well.

I just cut lots of strips and put layer after layer on until it reached the correct depth. The material I chose to pack it with ended up being double sided sellotape. The solution we came up with was to pack something into the space around the edges of the joystick base and then trap it but putting some wooden bars under it which would drill into the 18mm thick surround. But we were nervous that this might not be strong enough as it was only 9mm thick in that area now and we knew the joysticks would be getting waggled a fair but (oo-er – Ed). The easy way is to screw from below and put screws into the control panel from underneath.
ARCADE CONTROL PANEL MAME HOW TO
After this, however, the problem was how to attach it to the control panel. My father-in-law then used that line as a guide and routed the area out to a depth of about 9mm, halfway into the depth of the control panel. I took the joystick apart and then drew round the joystick base on the underside of the control panel. The reason for this is that the joystick base is quite thick and if you just have the base underneath the 18mm control panel wood then you lose 18mm of your joystick shaft length. One of the hard bits that I certainly couldn’t do myself on the control panel, because I don’t have a router, was to route an inset into the bottom of the control panel for the joystick base to fit into. I also used it for my joystick holes and the size was fine. I think I mentioned before but I used a 28mm spade drill bit. Then just be very careful that you drill straight when drilling the holes and don’t slip. I think I used the sharp point of an old spade bit. Then it’s just a simple case of laying this over your control panel and using something sharp to mark the centre of your button holes onto your control panel below. I then cut them out and sellotaped them together. They wouldn’t fit on an A3 sheet of paper so I had to scale them up in Photoshop to 1:1 scale and then split it into two images and print these out on A3 paper each. I went for the Sega Player 2 layout in the end. Use one of these tried and tested layouts. I had found the great Slag Coin website which has lots of button layout based on proper machines and anthropomorphic testing for hand sizes etc. I knew the placement would be very important and I wanted to get it absolutely right. So the first thing I actually had to do was to cut the holes for the joysticks and buttons.

I had got the bits of wood cut by B&Q and I’m pretty sure these were exactly right and were good to go with no changes. Now, I’ve got no experience at all of curving edges of bits of wood or of attaching bits of wood at angles, so I knew from the start that I would have to get help from my father-in-law for this bit.įirst things first though. But it wasn’t as ‘simple’ as putting two bits of wood together at 90 degrees and curving the edge, because the top of the control panel is actually at an angle. I think most of the curved control panels in actual arcade machines are made from metal, but I knew I had to do mine from wood. I just thought the curved front looks so cool, particularly when you have a nice vinyl sticker with artwork that accentuates the curve. A lot of people build control panels that are square but I stubbornly wanted to recreate the curved front of the Joust cabinet I was basing my machine on. I had a specific idea in mind for the control panel. To be honest, the control panel was one of the parts of the build I was most nervous about.
